Application Spotlight
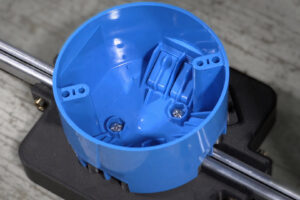
A machine builder approached Visumatic with a fastening application for fully automated assembly with an aggressive throughput requirement. The end user had a legacy product that required a screwdriving robot, automatically feeding and driving, one per cycle, a #8-18 x 1/2” long cross-recess drive pan head screw tightened at 15-20 in/lbs torque to assemble an electrical ceiling box to slide installation bracket. There were two drive locations per box, both in a vertical down drive plane.
The components would be fed, oriented, and placed in the fixture by the machine. First the metal crossbar and bracket that receives the screw, and then the injection molded box to which they attach. The box is made up of complex high-wall surfaces.
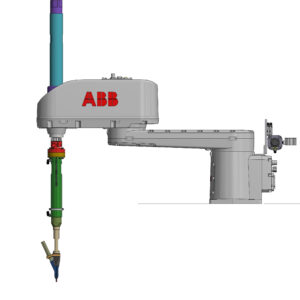
The Viper MBC package was selected to perform the high-speed robotic screwdriving. Reaching down inside the open cavity was handled by the built-in z-axis quill motion. The theta-axis worked to quickly orient the tooling tip for controlled access to the tight clearance installation points. Finally, the feed direct to tip function saved valuable cycle time by limiting takt time robot moves to strictly point-to-point.
The machine builder then brought their favorite brand of SCARA robot and the customer-specified screwdriving motor. This allowed their team to focus on their core parts handling work while Visumatic supplied a rapid deployment fastening solution. They delivered their assembly machinery to the end-user under budget, with faster throughput, and right on time.
See the full range of SCARA fastening options on the Viper MBC Screwdriving Robot page.
This screwdriving robot was delivered ready to install and program.