Multiple Robots Deliver Iron-Clad Quality Control without Raising Headcount
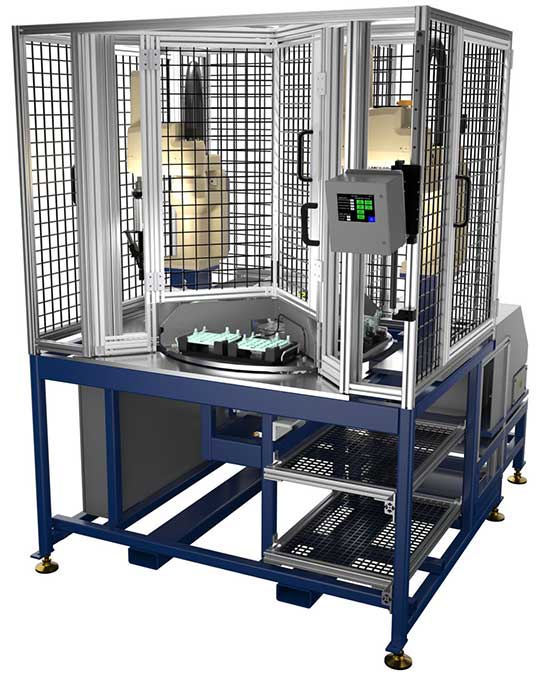
A Tier 1 automotive interior trim manufacturer was tooling up for a new model year. The final assembly plant wanted the parts delivered in sets as they were to be vehicle installed on the line. Visumatic was asked to review the 3 assemblies, as well as their sub-model variants, to see what fastening options would provide the desired batch product throughput.
Visumatic built an automated machine with Poka-yoke part fixtures capable of receiving the full variety of trim parts and mounting them to a four-station rotary indexing system. This way, the full range of assembly operations could be performed, including the addition of a part inspection station.
The target Takt time was achieved by incorporating two SCARA robot systems. The first robot station automatically feeds and drives up to ten M4 x 12mm long cross recess drive pan head screws to the required 1.4 Nm torque using the Viper MBC robot screwdriving system. Another station fed and inserted plastic clips vertically down by mounting the VIM-700 clip insertion module onto the second SCARA robot.
By utilizing the fast point to point robot moves and breaking out the work by type, Visumatic was able to produce the required part sets under the target cycle time. Having a universal smart fixture design kept the head count to a single operator who enters the cell with muted safety light curtains to load and unload the parts. The trim manufacturer was able to deliver a greater value to their automotive customer while increasing the level of quality control inherent in Visumatic’s engineered assembly platform.
See additional quality assured fastening approaches on our SCARA robotic screwdriver page.
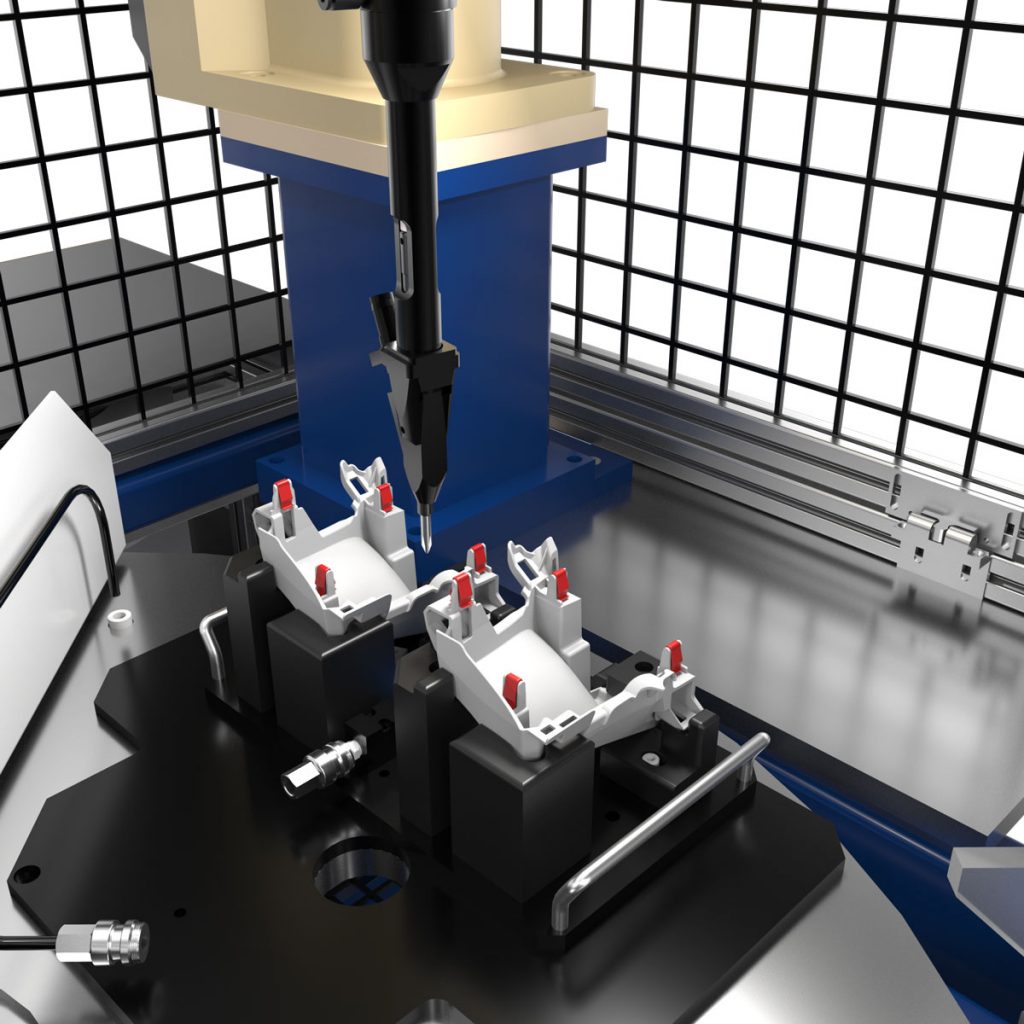
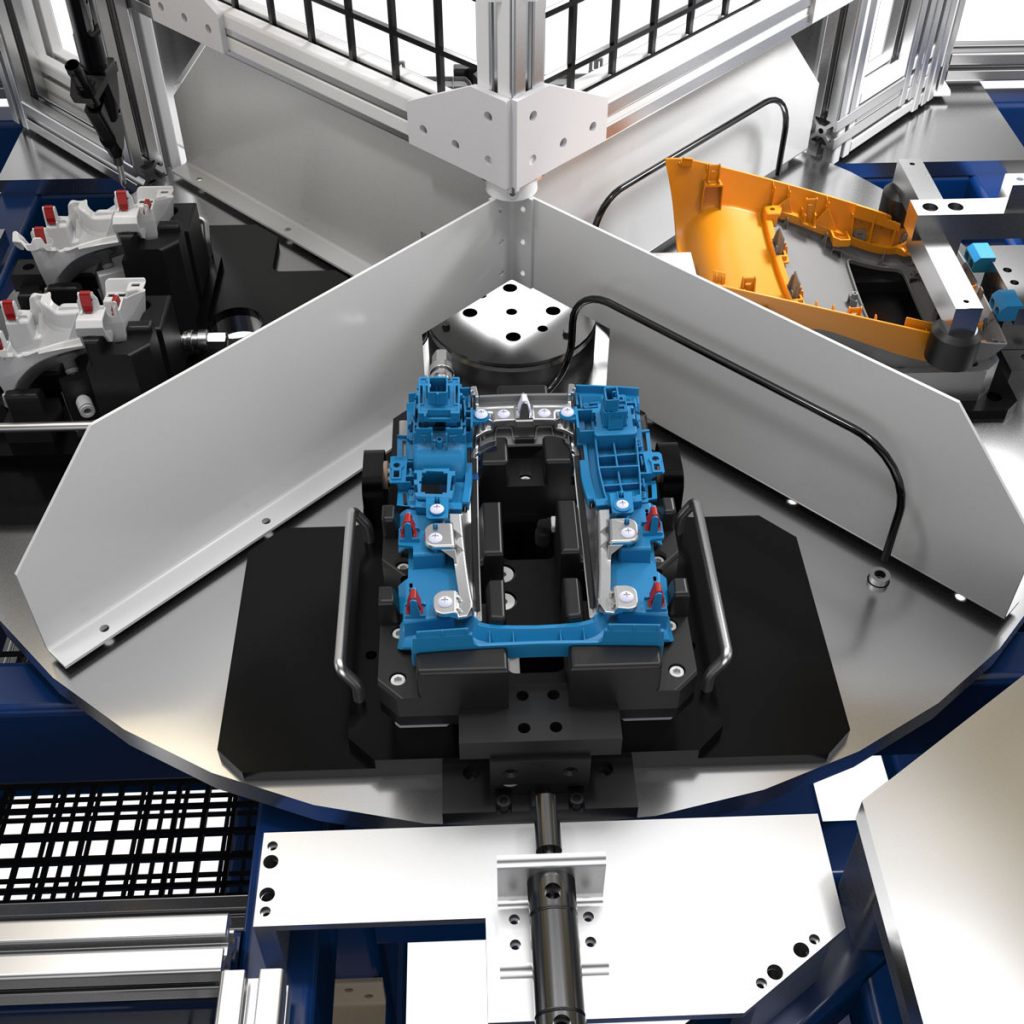
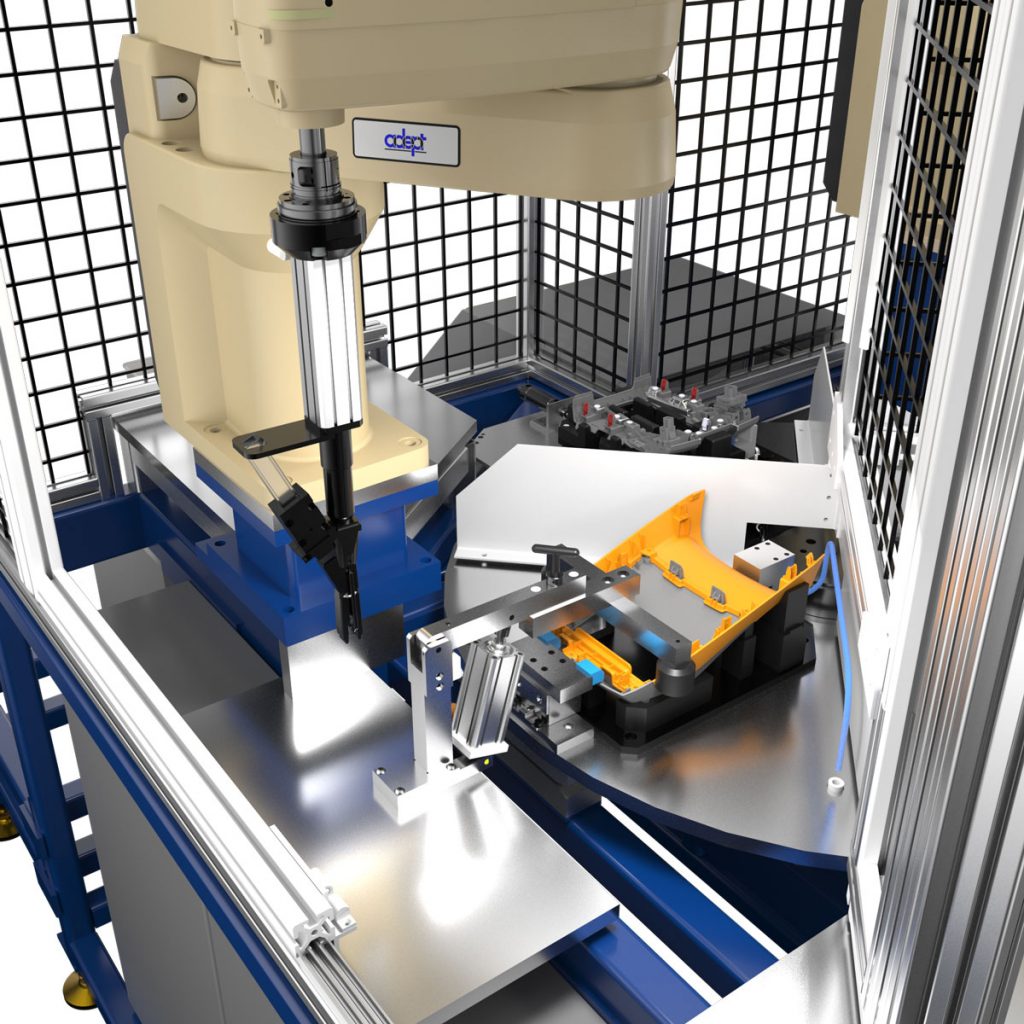