Robot Screwdriver & Clip Inserter Machine Provides Next-Level Quality Control
Application Spotlight
Along with a mid-model design change, this automotive interior trim maker saw their production target triple. Already struggling with some quality concerns, they met with Visumatic to review the assembly process and explore options.
All work was previously done manually in separate workstations with the metal clip installed first, then the parts were transferred and finally the mounting studs were positioned in the socket and driven. In addition to requiring multiple assembly steps, the manual operations were causing quality control headaches due to missing fasteners, unseated clips, and stripped studs.
The Visumatic engineering team developed a concept to provide the greatest benefit possible while staying under budget. The machine combined all work into one station by utilizing a cartesian X-Y-Z robot, reducing the required head count by one. Both fasteners were blow fed into the work envelope utilizing the X-axis to carry both fastener spindles, with the VIM-600 metal clip insertion spindle on the Z-axis actuator to accommodate the various clip tower heights.
After noting the material flex of the thin bezel material, a dual nest part fixture was designed to cradle the part and provide multiple point backing for each fastener installation. In addition to protecting the no-mar finished surface, the clamping smart fixture provided accurate depth detection for both the clip insert and stud driving.
The fixture was mounted to the Y-axis actuator using a disjointed topography. This allowed elimination of a gantry component while maintaining fast robot movement speed, minimizing the machine footprint to save factory space.
The fastener feeder systems were mounted on an independent table, giving placement flexibility to the plant material handlers. The machine delivered next-level quality assurances through process monitoring and sequence verification by the PLC machine control.
Clip presence and seating depth were verified by the built-in VIM-600 insertion sensors. The stud was fed to the VPD Power Driver and driven to torque and angle. The results of each fastener install were graphically displayed in real-time on the full-color HMI control screen, along with standard production data.
With quality assured and production targets met, now their only worry is getting them out the door. See more fastening configuration options on our cartesian robot screwdriver page.
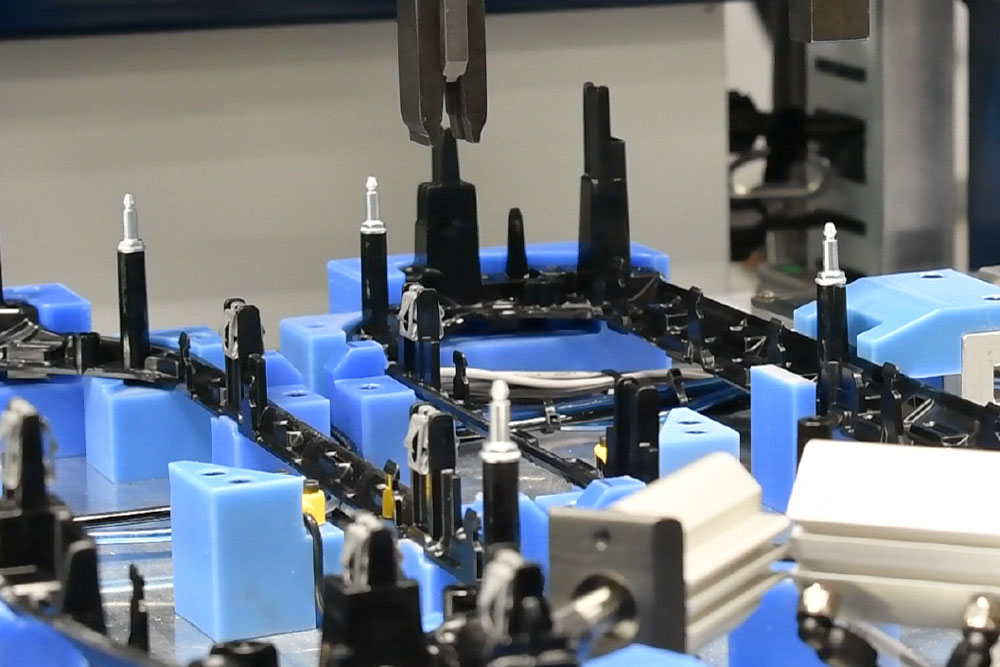
Dual fastening spindles, one for mounting stud and one for metal clip insertion on Z-axis actuator.
Advance cartesian robot screwdriver with clip insertion video.