White Goods Manufacturer Smashes Productivity Barriers
Machine Builder Spotlight
An appliance manufacturer’s in-house build group was looking to clear the bottle neck on their washing machine assembly line. Their kaizen plan was being held up by this agitator trunnion install process which was limiting a production rate increase. After consulting with Visumatic, the decision was made for them to fully automate the fastening using three (3) single spindle VPD Power Driver screwdriving systems.
The current process had a single operator driving screws one at a time with a manual gun on a torque arm. The drum and agitator were presented on a palletized conveyor, then manually indexed on three-position rotary fixture. The operator drove 3 pairs of thread-lock screws, two per trunnion attachment point, for six screw drives total.
The machine builders removed the operator completely and replaced the indexer with a rotary servo. They positioned the Visumatic Power Drivers about the radial axis opposite each agitator arm. All spindles automatically fed and drove their screws simultaneously, the servo indexed, and then each spindle drove a second screw to complete the assembly.
They successfully increased throughput at this station by 66% blasting this major bottleneck out of the water. In addition to opening up possibilities on the line for the Kaizen team, the group was able to achieve a modest ROI by reducing the head count by one. Re-work due to operator error was eliminated while further improving product quality. The implementation was able to bolster quality by providing full SPC data reporting including the torque and angle of each screw driven.
By selecting the heavy duty 7 series, they are confident the componentry can hold up to the rigors of operating on a metal joining assembly line. See the full range of screwdriving spindle options on our VPD Power Driver page.
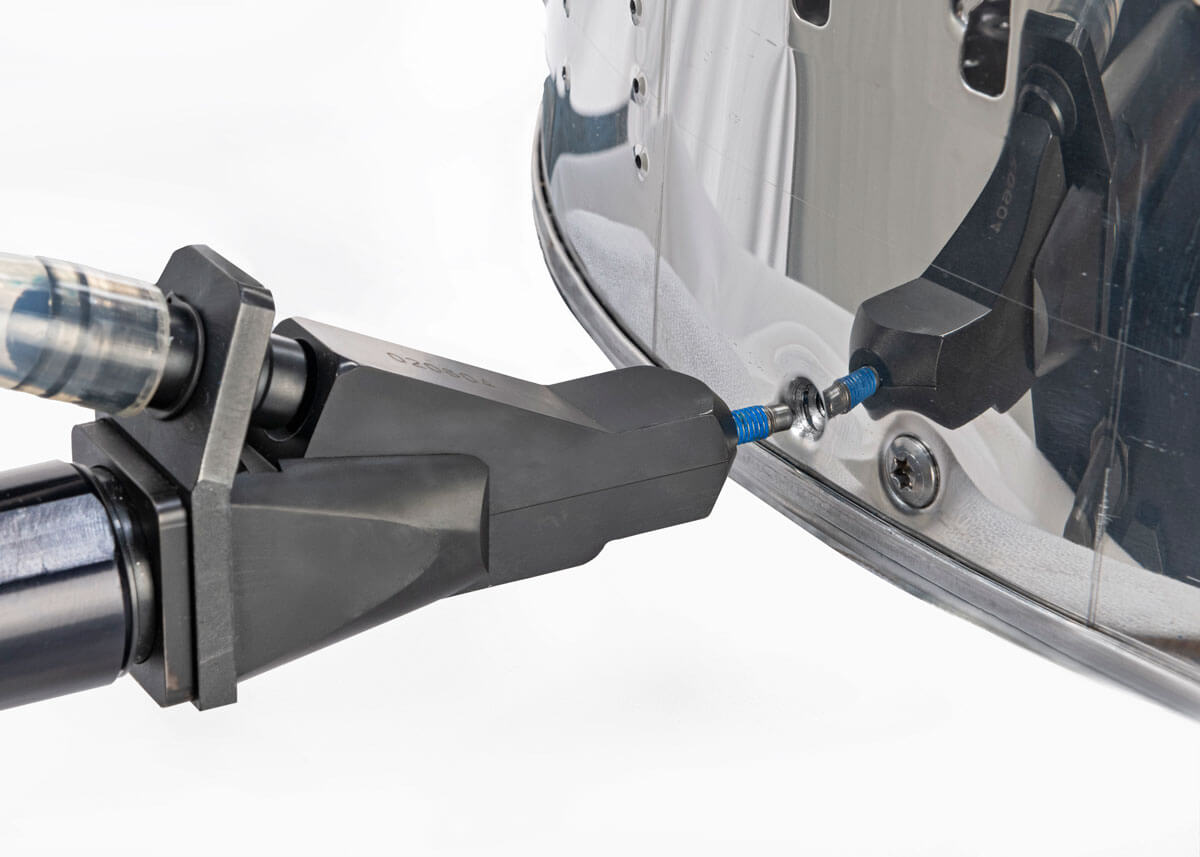